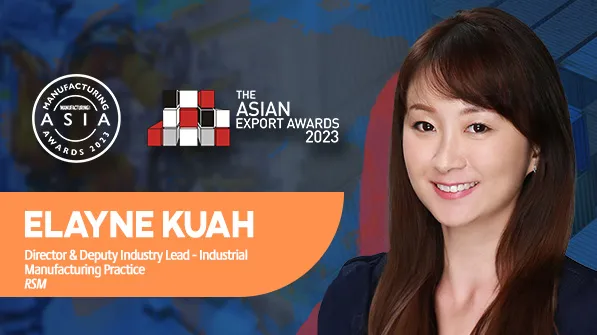
Continuous risk management crucial amidst evolving business needs, market changes – RSM Singapore’s Elayne Kuah
Companies must stay informed about changing regulations and market conditions, as well as maintain open communication with providers to manage risks and adjust when necessary.
The Asian manufacturing and export sectors are pivotal engines of economic growth and global trade. Spanning a diverse range of industries, these sectors have propelled many Asian economies to prominence on the global stage. The region's strategic geographic location, skilled labour force, and infrastructure development have made it a manufacturing powerhouse, producing a substantial portion of the world's goods.
Elayne Kuah, Director & Deputy Industry Lead - Industrial Manufacturing Practice at RSM Singapore, has an impressive career trajectory that speaks volumes about her expertise in the realm of industrial manufacturing and export. With her tenure at RSM Singapore since 2009, she has provided invaluable services to public-listed companies and privately owned enterprises across diverse industries, including manufacturing, F&B, and retail.
Her clientele extends to financial services, encompassing captive insurance companies, insurance brokers, and financial advisers. Kuah's professional journey also includes handling grant assurance engagements, IPOs, and RTO assignments for her clients.
Kuah’s expertise shone through as she delved into her insights on the manufacturing and export sectors. In this interview with Kuah, she talks about achieving operational excellence and innovation, as well as optimising risk management for export operations, amongst others.
Drawing from your experience across diverse industries, how can manufacturing companies achieve operational excellence whilst also fostering sustainable growth and innovation?
Manufacturing companies can incorporate several steps to achieve operational excellence whilst fostering sustainable growth and innovation. Some key steps that, in our opinion, contribute to achieving these goals include the following:
Invest in technology and automation to optimise manufacturing practices and processes. Companies should continuously invest in technology to help streamline manufacturing processes. Investments in technology also contribute to and support innovation, and the resulting automation helps reduce employees’ workload by eliminating tedious and repetitive tasks that employees may find burdensome.
Foster a culture that encourages feedback and innovation. Companies can nurture a positive culture by empowering employees, providing training, involving them in decision-making processes, supporting their inputs for innovation, and streamlining processes that optimise their own productivity. Employees are the frontline workers on the ground, and they may have insights into pain points, allowing them to share invaluable information.
Demonstrate commitment from the top leaders. Leaders serve as the driving force that ensures changes are implemented consistently and resources for investments in technology are allocated adequately. Their commitment is essential to achieve the company’s goals.
Manufacturing companies need to be strategic in their approach to achieve all three goals of operational excellence whilst fostering sustainable growth and innovation.
How can manufacturing companies collaborate with financial advisers, insurance providers, or captive insurance companies to optimise risk management and ensure seamless export operations?
Manufacturing companies should first assess their needs and identify risks associated with their manufacturing processes and export operations. They can engage and collaborate with financial advisers and insurance brokers or providers to review their risk management strategies, develop risk mitigation strategies, and also work with them to tailor their insurance coverage to address their export risk and asset risk.
Managing risks is an ongoing process, given the evolving business needs and changing market conditions. Hence, it is also important for companies to stay informed about the changing regulations and market conditions and maintain regular and open communication with their providers so as to manage their risk by adjusting the coverage when necessary.
Where there are a group of companies involved, captive insurance can also be considered as a strategy to optimise risk management. A captive insurance company refers to a subsidiary company within the group that is formed to provide risk mitigation services for its parent company and/or its related entities. Captive insurance allows companies to create their own insurance company to cover specific identified risks, thus customising coverage. Also, there may be tax incentives for captive companies, which may result in tax savings for the group. However, companies should first evaluate the feasibility and potential benefits of establishing a captive insurance company, taking into account regulatory compliance requirements, resources, and cost-benefit analysis.
How can manufacturing companies effectively balance the need for compliance with the agility required to navigate changing international regulations and maintain export competitiveness?
The main objective of a compliance review is to add value to the company. However, this can become challenging for many companies because staying in compliance with all rules and regulations burdens and often forces them to compromise on agility. Companies must understand that not all jurisdictional requirements are mandatory. Therefore, there is a need to evaluate these requirements and rank them in accordance with an urgency and importance matrix. Following this, resources can then be allocated accordingly to ensure compliance. The changing international regulations are inevitable and companies need to assign dedicated resources to ensure compliance.
Earlier, we mentioned investment in technology and automation. Companies can review their processes to identify repetitive compliance tasks that can be automated by technology to improve efficiency and reduce the risk of “human” errors.
Companies can also look to collaborate with industry peers. There are various industry groups and trade associations that provide guidance to navigate regulatory challenges and share best practices related to compliance. These groups also organise networking activities that facilitate collaboration with peers to share best practices, which companies can tap into.
Lastly, for companies to maintain export competitiveness, they should explore Free Trade Agreements (FTA) together with their existing supply chain and the revenue contribution per geographical location.
Where help is required, engage the experts. They can conduct compliance audits, provide meaningful insights, and offer guidance on navigating complex international regulations.
How can manufacturing companies use ISO inspections as opportunities to not only ensure compliance but also drive sustainable manufacturing practices?
The International Organisation for Standardisation (ISO) standards provide a structured framework for companies, covering a wide range of areas including quality management systems, product management, environmental management, information technology, and more. ISO inspections involve companies assessing their compliance with ISO standards through audits.
Companies can leverage ISO standards and inspections as opportunities to ensure compliance and promote sustainability practices.
This can be achieved by integrating sustainable manufacturing objectives that align with the company’s goals into the Quality Management System. Furthermore, companies can use inspections—both external and internal—as opportunities to review and assess the effectiveness of sustainable practices, identify areas for improvement, and take corrective actions as needed. By doing so, they not only ensure compliance with regulatory requirements but also promote sustainable manufacturing objectives, enhancing the company's brand reputation and securing future earnings through stakeholder loyalty and advocacy.
Manufacturing companies can also consider obtaining certification to enhance their compliance with environmental performance standards. For instance, ISO standards such as ISO 9001:2015 for Quality Management and ISO 14001 for Environmental Management, provide a framework for achieving both compliance and sustainability objectives.
What specific qualities, achievements, or innovative approaches do you look for in manufacturing and export initiatives that make them stand out as exceptional and deserving of recognition?
Specific criteria and qualities that would make a business stand out in relation to manufacturing and expert initiatives would include:
Companies that have demonstrated commitment to sustainable supply chain management and practices, including waste and energy consumption reductions, and have made a significant positive impact not only on stakeholders but also on communities make them deserving of recognition; those who have made investments in technology to ensure efficient sustainable manufacturing processes and quality of products; and businesses that have implemented strategies to grow their presence in international markets or enter new export markets.