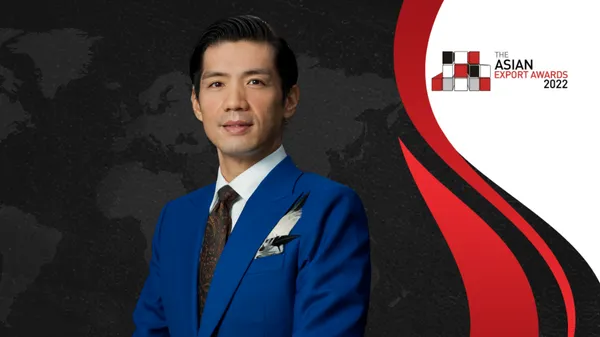
Leaders should take the first step in embracing disruptive digital innovations
Deloitte Singapore’s Jeremy Huang, says manufacturing leaders can start by unifying communications across the business.
Change can come with good and bad things, and the disruptive changes of digitalisation brings plenty of both to the manufacturing industry.
That is why Jeremy Huang, Director of Corporate Finance Advisory at Deloitte Singapore, believes that it is important for leaders to take the first step towards digitalisation and show the way forward through partnering with stakeholders and finding the right balance for every aspect of the business.
Jeremy has over 10 years of experience in Mergers & Acquisitions across manufacturing, industrial, mining services, and healthcare sectors.
He has advised on transactions in Australia, Tanzania, Malawi, Singapore, Malaysia, and Indonesia, including the privatisation of three SGX-listed manufacturing companies.
Jeremy observed that with the rapid integration of digital transformation into the industry, large manufacturers with high margins, processes, and intellectual property ownership from Europe and US are partnering with their customers to design and engineer innovative solutions through a combination of manufacturing and technology solutions to support challenging products across multiple markets.
“Finding the right balance that maximises revenue, reduces costs, increases efficiency, and improves flexibility will spur manufacturers to incorporate new technologies and stay competitive in the global marketplace,” Jeremy said.
In a quick chat with Manufacturing Asia, Jeremy discussed the edge of digitalisation for the manufacturing industry, the challenges that industry players are encountering in the post-COVID-19 world, as well as how to overcome the risks brought about by digital transformation.
Based on your experience, what can you say about the digital transformation of the manufacturing industry in Southeast Asia? Where do you think is the edge of digitalisation for manufacturers?
Rising economic nationalism, US-China trade relations, the COVID-19 pandemic and the supply chain crisis have created vast opportunities for Southeast Asia (SEA) manufacturers to capture the potential of Industry 4.0. Yet, an Oracle survey suggests that technology professionals working in the manufacturing sector at SEA perceived their companies are lagging to adopt digital technologies even though the industry contributes over 20% to the GDP of the individual markets in the region. We have observed that a few leading SEA manufacturing companies have heavily invested in digitalisation but may not have done so wisely to achieve optimal profit margin. For instance, a Singapore machining and engineering services company made substantial investments into advanced manufacturing equipment and associated digital control and reporting systems. In doing so, it was able to significantly reduce direct costs through automation and had a healthy cash gross margin and EBITDA margin.
However, accounting for depreciation, gross profits were low and net profits suffered. This is a cautionary tale for companies looking at their own digital transformation, to ensure that capital investments are measured and potentially staged over a longer period of time. Nevertheless, this is not to say that manufacturers should not embark on digitalisation as there are credible successful examples in Southeast Asia. In Singapore, with the recent support from the government to pave the way for digital transition in the post-COVID-19 economy, we are seeing a positive impact on the manufacturing players. For instance, a precision engineering company operating in Singapore with a larger company headquartered in Europe has recently successfully partnered with a Singapore government research agency to automate and streamline internal processes which has boosted its efficiency and returns.
Finding the right balance that maximises revenue, reduces costs, increases efficiency, and improves flexibility will spur manufacturers to incorporate new technologies and stay competitive in the global marketplace.
What strategies are you seeing firms adopting to ride the trend? What are the challenges companies faced throughout the transformation? How did they overcome them?
We observed large manufacturers of scale with high margins, processes, and intellectual property ownership from Europe and US partnering with their customers to design and engineer innovative solutions through a combination of manufacturing and technology solutions to support challenging products across multiple markets. People and processes are often the key barriers to digitalisation – when embarking on the digital transformation journey, companies may find themselves facing a lack of digital skills in their workforce. Conversely, customers and/or manufacturers who are operating in a low margin industry with tight cost controls have adopted a wait-and-see approach.
Strong government support for Industry 4.0 which aligns with the industry needs, entering global partnerships, embedding technology, a mindset shift especially amongst the upper management, and improving digital literacy are some of the push factors to accelerate technology adoption in the SEA manufacturing sector.
As the COVID-19 pandemic left a massive effect globally and markets are now starting to recover from the crisis, what are the possible opportunities for manufacturers and exporters? How can companies develop new export markets to expand their business reach?
The COVID-19 pandemic has led several global manufacturers and exporters outside of SEA to consider accelerating the adoption of automation and robotics due to labour shortage, more stringent Service Level Agreement and Environmental, Social & Governance requirements and increasing demands for e-commerce. These days, many manufacturers are embracing end-to-end automation to streamline production processes, which allows players to have more recurring revenue streams, stable profit growth, accelerated return of investment, and greater customer satisfaction. Given that more countries are imposing stricter laws and regulations for exporting goods, digital transformation will be able to help increase reliability and improve safety measures for manufacturing and supply chain processes.
In SEA, we have observed a lower uptake and in fact, some of the digital innovation and automation in manufacturing has been led by private equity-funded manufacturers who are seeking to reduce labour costs, de-risk operations, and engineer a defensible and compelling growth story for their exit.
In the digital era where the transition of the digital trade era is quite challenging, how can exporters and manufacturers overcome the risks of the transformation?
Any transformation is risky and risky endeavours require buy-in and support from senior management. Leaders in the export and manufacturing sectors need to shift their mindset to embrace the disruptive impact transformation will have on the industrial space and global trade. They can start by developing a simple yet robust and unified communication and messaging for employees to collaborate and work seamlessly across different functions at different locations to implement digitisation.
In addition, companies typically do not have a digital transformation team or office to bridge technology skill gaps or bring all business units together to drive such transformation. Hence, they can consider hiring external professionals and consultants to assist with the journey.
Following this approach, manufacturers and exporters can think about implementing modules in their Enterprise Resource Planning to plug into digital trade platforms and build out the correct integrations into the company’s existing systems with their employees, customers, and suppliers.
As a judge in the Asian Export Awards, what would be your criteria for selecting the winners?
Resilience during the uncertainties and an adaptable mindset that looks forward to the ever-changing market and trade in the post-COVID-19 economy are prerequisites to triumph in the digital trade era.