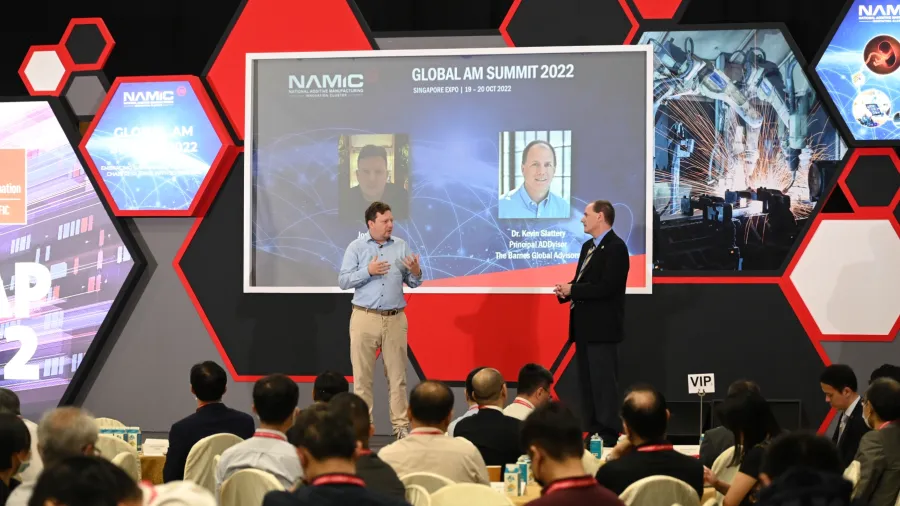
Is additive manufacturing ready for mass production?
The proposition entails diving into various manufacturing aspects.
Questions on whether the additive manufacturing industry is prepared for mass production has amassed as more businesses dip their toes in the field.
Kevin Slattery, a principal advisor for The Barnes Global Advisors, said the answer depends on what industry the company is in, as it will translate to different possible outcomes.
“In some ways, it depends on what the industry is. If you're looking in the consumer goods, electronics, or certain areas like automotive where you [will possibly deal with] hundreds or thousands of aircraft engines or aircraft structures… So, you know, what the definition of mass manufacturing depends [on the industry],” he said.
For Joris Peels, vice president of 3Dprint.com, success depends on the business involved in mass manufacturing.
He said there is the possibility of having a very low margin or customers who will negotiate down to a loss. The volumes may be very high but not very profitable.
“I think compared to other businesses…For example, metal medical implants and stuff like that [are a] much more profitable business. It's much more future-proof [and is] suited for mass adoption,” Joris said.
Kevin agreed, adding that medical implant innovations are taking the lead in the industry today.
“I came across medical implants and medical innovations. If you look across the industry now, if you look at the square meters of the facilities and the size of its printer, they're operating [for about] 2,000 to 8,000 hours a year,” he said.
Another industry that can benefit from this is those involved in automotive. Kevin had observed that certain cars have been utilizing 3D parts and consist of hundreds of thousands of parts.
The challenge for manufacturers of these automobiles is to meet the requirements to provide for all these parts.
Joris said that despite the different challenges faced by the industry, including the competition between those involved in additive manufacturing, firms must always keep in mind how to provide good and functional parts.
“The first step is to figure out what you want to do. If you're going to take the same shape and have seen it [elsewhere], it’s good for you to learn what you don't know and to gain knowledge,” he said.
“But you really have to consolidate parts, and then you have to figure out what your values are going to be and what kind of equipment and what kind of process will get you there,” he added.
Given that the industry is growing rapidly, Kevin said new opportunities will also come up.
“There are a lot of good contract manufacturers out there now, and you work with them to figure out what you want. You will gain experience on the design side and the engineering side,” he said.